cart for my engine
Re: cart for my engine
Hey Nudge that´s such a beautiful machine! Are you planning to make a video of it in full action? Would be great!
Re: cart for my engine
Although I have done very little iron it seems to me that is you have done brass which you have it is not a lot different. Your furnace of course has to be able to make the few extra hundred degrees, again your burner will have no problems. It is a little hotter of a potato to handle so if when doing brass you 'feel' the heat then you may need to compensate with longer tongs or better gloves as the radiant heat is pretty intense. The use of shaded eyeware is also a consideration as iron is quite bright when ready to pour.
Again this is from limited knowledge on the subject but I dont think the cover is nearly as important with iron as with brass. Also make up a crude skimmer and dont use your regular tools, for me iron slag tended to build up on anything stuck into the pot making it a much more disposable type of tool so if you have a nice skimmer dont use it.
Looking forward to hearing the results of your pour, I really want to make the time to do a die that I have had on the back burner for a long time to do aluminum gravity casting into.
Again this is from limited knowledge on the subject but I dont think the cover is nearly as important with iron as with brass. Also make up a crude skimmer and dont use your regular tools, for me iron slag tended to build up on anything stuck into the pot making it a much more disposable type of tool so if you have a nice skimmer dont use it.
Looking forward to hearing the results of your pour, I really want to make the time to do a die that I have had on the back burner for a long time to do aluminum gravity casting into.
I'd rather laugh with the sinners than cry with the saints the sinners are much more fun...
Muller
Muller
Re: cart for my engine
Yes, dedicate a crucible for Iron. It won't be much good for anything else. A little charcoal cover, some Limestone(dry) for flux and a little FeSi, if you can find some, to help with fluidity. Or, just use thin castings in the melt, they should be pretty high Silicon.
quando omni flunkus moritati 

Re: cart for my engine
Looking good.
For 3D CAD it might be worth getting turbo cad 15 pro. It's around GB£180 but is well established package, it's cheep because they are up to version 18 now, but 15 is well capable. I can get you started on 3D with it, I'm self taught and it took a while but I've just had a whole new set of plastics SLA prodcued from my drawings and we are now going to hard tooling from the files produced on 15 pro. I'm more than happy to talk you through the build process if you go that route. GCode, I know little about but once you have an STL or IGS file I believe there are good packages to produce the code.
For 3D CAD it might be worth getting turbo cad 15 pro. It's around GB£180 but is well established package, it's cheep because they are up to version 18 now, but 15 is well capable. I can get you started on 3D with it, I'm self taught and it took a while but I've just had a whole new set of plastics SLA prodcued from my drawings and we are now going to hard tooling from the files produced on 15 pro. I'm more than happy to talk you through the build process if you go that route. GCode, I know little about but once you have an STL or IGS file I believe there are good packages to produce the code.
Re: cart for my engine
A question for Jammer if I may, I've melted Cast Iron before and have access to FeSi if I need it but haven't so far. What i've been melting is old Bearing housing and Gear Box cases that I pick up around Asphalt plants while working on them. I have a lot of slag that comes off of the melt but thats understandable due to me not cleaning them (pressure washing the grease and crud off), I just either bust them up or cut them up in the band saw.Jammer wrote:Yes, dedicate a crucible for Iron. It won't be much good for anything else. A little charcoal cover, some Limestone(dry) for flux and a little FeSi, if you can find some, to help with fluidity. Or, just use thin castings in the melt, they should be pretty high Silicon.
I mostly will after melting and pouring, after pullling the casting from the sand put it in the furnace to cool down over night and I get good gray machinable iron.
Heres the question, I have been told and everything I have read say's that limestone doesn't do anything to the lron after its been through the blast furnace, that it is used there to fluidize the slag. I have tried crushed limestone screenings from an Ashpalt plant once but all I found was the stone still in the bottom of the crucible. The other thing that I can't find any information on is what type of limestone is used as a fluxing agent?
And
FeSi can be had from BCS here in the states, Around 25 dollars for like a pint containers worth I belive, haven't checked the price lately.
David
David and Charlie aka the shop monster
If life seems normal your not going fast enough" Mario Andrette
If life seems normal your not going fast enough" Mario Andrette
Re: cart for my engine
When you did your casting how did you know when it was hot enough to pour?
With brass / bronze I use the dip the steel rod trick, if the rod comes out clean then it is good to pour
With brass / bronze I use the dip the steel rod trick, if the rod comes out clean then it is good to pour

I like to build "Stuff" using Stuff that costs Stuff All!
Re: cart for my engine
when the iron starts to melt it will leave a husk of the former piece that you put in the furnace, I don't know why but it does and if you don't know it you will think that the stuffs not melting, so once the iron is yellow I will start to poke it with a stainless steel rod that I keep by the furnace too see if I can push the piece apart.
After that its pretty much just getting the amount that you need melted and making sure that all thats in the crucible has turned liquid. A guy that i know who has melted a bunch of iron says that sparks should be coming off the iron, but when its that hot (over 2700 degrees) your burning the carbon out. along with some of the Silicon. Some say to flux, I don't as the slag off the Iron is pretty corssive to the refactory, and to your crucibles. One thing is for sure once you melt iron in a crucible you won't melt anything else in it.
I don't have a Probe to measure as high as you have to go to melt Iron, and my first furnace that I made and melted iron in took a pretty good beating on the lid which I had made out of White Brick, its still usable but I have a bigger one now that I use mostly because the lid swings over the side.
Start off with only a couple pieces in the crucible with others laying on the lid around the exhaust to preheat, I run propane using a Vacumn Cleaner blower for air, I know its way more air then I need but I got lots of propane. My burner is kinda funny in that I have the blade off of a muffin fan in the tube to spin the air just in front of where the gas enters.
My big furnace is made with the wall being 2600 degree refactory 3 inches thick, this cause it to take a while to heat up but once it does it doesn't take long to melt a A10 to within 1.5 inches of the top. Slag; you will want something that you can pretty much pitch, you can use a piece of rebar to kinda wrap the stuff up on it like cotton candy when you pull it out I just bust it off your not going to get all of it so don't try. The best thing is if you can handle the shank by yourself is to have someone else use a board to hold the slag back from going into the mold. I know a lot of people try to scrape their Crucibles out after pouring with iron its a differant story becasue the stuff sticks big time, just leave it and use whats left in the crucible to get the heal started on the next pour. sometimes after the Crucible cools whats inside will pop loose, if it doesn't leave it becasue it will peel out a layer of the crucible if you start prying around on it.
You can use Clay Graphite, or anyway it will take the temperature for a while, but if your going to melt a bunch get a Silicon Carbide much safer. this picture is of me pouring iron for a backing plate for my 12 inch lathe. I think that Crucible had two melts on it when that picture was taken, Notice the wet looking place down the side thats from slag running down it.
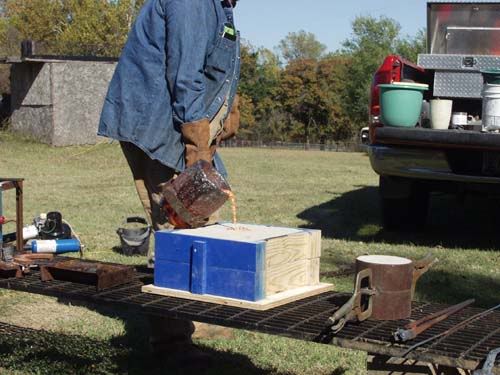
this is up to you but I would be sure and put a piece of cardboard on the plith block under the crucible otherwise the crucible may melt to it and thats no fun when your half way out and all of a sudden you have and extra 4 inches to come up to get it out. That was a fun melt me swinging that 20 pounds of iron around trying to get that damn block to fall off.
Anyway to answer you question when your furnace is just about white hot is when your gonna start melting iron, around 2600, break your source up into small pieces they melt better heat up faster, I don't use any cover cause I don't know what will last in the heat and slag, I may try oyster shells I can get them crushed at the feed store. they say marble chips will work and melt and help fluidize the slag, easiest is to skim it after you pull the pot, and what you can't get have someone hold it back from the lip with a board.
Be super safe
David
After that its pretty much just getting the amount that you need melted and making sure that all thats in the crucible has turned liquid. A guy that i know who has melted a bunch of iron says that sparks should be coming off the iron, but when its that hot (over 2700 degrees) your burning the carbon out. along with some of the Silicon. Some say to flux, I don't as the slag off the Iron is pretty corssive to the refactory, and to your crucibles. One thing is for sure once you melt iron in a crucible you won't melt anything else in it.
I don't have a Probe to measure as high as you have to go to melt Iron, and my first furnace that I made and melted iron in took a pretty good beating on the lid which I had made out of White Brick, its still usable but I have a bigger one now that I use mostly because the lid swings over the side.
Start off with only a couple pieces in the crucible with others laying on the lid around the exhaust to preheat, I run propane using a Vacumn Cleaner blower for air, I know its way more air then I need but I got lots of propane. My burner is kinda funny in that I have the blade off of a muffin fan in the tube to spin the air just in front of where the gas enters.
My big furnace is made with the wall being 2600 degree refactory 3 inches thick, this cause it to take a while to heat up but once it does it doesn't take long to melt a A10 to within 1.5 inches of the top. Slag; you will want something that you can pretty much pitch, you can use a piece of rebar to kinda wrap the stuff up on it like cotton candy when you pull it out I just bust it off your not going to get all of it so don't try. The best thing is if you can handle the shank by yourself is to have someone else use a board to hold the slag back from going into the mold. I know a lot of people try to scrape their Crucibles out after pouring with iron its a differant story becasue the stuff sticks big time, just leave it and use whats left in the crucible to get the heal started on the next pour. sometimes after the Crucible cools whats inside will pop loose, if it doesn't leave it becasue it will peel out a layer of the crucible if you start prying around on it.
You can use Clay Graphite, or anyway it will take the temperature for a while, but if your going to melt a bunch get a Silicon Carbide much safer. this picture is of me pouring iron for a backing plate for my 12 inch lathe. I think that Crucible had two melts on it when that picture was taken, Notice the wet looking place down the side thats from slag running down it.
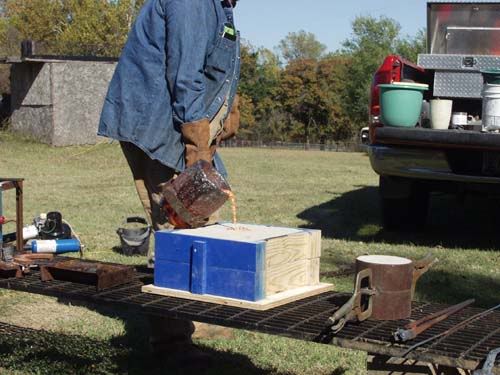
this is up to you but I would be sure and put a piece of cardboard on the plith block under the crucible otherwise the crucible may melt to it and thats no fun when your half way out and all of a sudden you have and extra 4 inches to come up to get it out. That was a fun melt me swinging that 20 pounds of iron around trying to get that damn block to fall off.
Anyway to answer you question when your furnace is just about white hot is when your gonna start melting iron, around 2600, break your source up into small pieces they melt better heat up faster, I don't use any cover cause I don't know what will last in the heat and slag, I may try oyster shells I can get them crushed at the feed store. they say marble chips will work and melt and help fluidize the slag, easiest is to skim it after you pull the pot, and what you can't get have someone hold it back from the lip with a board.
Be super safe
David
David and Charlie aka the shop monster
If life seems normal your not going fast enough" Mario Andrette
If life seems normal your not going fast enough" Mario Andrette
Re: cart for my engine
I used Limestone from the driveway in the assumtion that is makes the slag fluid and reduces the acidity so it's not so hard on the crucible. We use it in the Electric Arc furnace at work for Steel, along with anthracite coal as a cover. One of my jobs is to test the slag for acidity and for the levels of Calcium and MgO. I've been just using that at home in the smaller scale. I have some Fluorspar but I haven't used it, it's a very strong flux and I'm a little worried it may damage my furnace lining or the crucible. I used Ferro Silicon I got from work jsut because someone said it would make the Iron pour like water and it did. Would it have been any different if I hadn't used it? I don't know.
BCS may charge $25 a pound for the FeSi, my work pays $1140/ton, that work out to be .57 cents a pound, but we get 20 tons at a time.
The only thing worse than having your plinth come out with the crucible of Iron, is having half the plinth come out so you cant set it down or put it back or get the tongs, I just danced around for a bit and kind of tossed the crucible on to the flask. At least it was less than 10 pounds.
I don't think I'll pour Iron again by myself.

BCS may charge $25 a pound for the FeSi, my work pays $1140/ton, that work out to be .57 cents a pound, but we get 20 tons at a time.

The only thing worse than having your plinth come out with the crucible of Iron, is having half the plinth come out so you cant set it down or put it back or get the tongs, I just danced around for a bit and kind of tossed the crucible on to the flask. At least it was less than 10 pounds.

I don't think I'll pour Iron again by myself.
quando omni flunkus moritati 

Re: cart for my engine
I am just going by what I have learned from the melts that I have done with iron. my first melts were in a small A4 clay graphite crucible, which cracked bad enough that I could see the molten metal thru the cracks, still haven't figured out why it didn't run through.
The last time I melted iron I made the backing plate, the only thing I put in the crucible waw iron, borax isn't any good with iron that I know of and the only other thing that I had that might of been any extra help in the melt was brazing flux that I have. I can get Fluorspar but like you said its strong stuff and will erode the refactory and your crucilbe. The FeSi I would like to get some and try it, as its suppose to also help with the machineability of the iron. My long reaching plans for this hobby is to eventually learn enough that I can build from scratch a moderate size steam engine, but it looks like as much as there is to have to learn that I may be a very old man before I get there, but I am gonna give it one heck of a try.
So I guess that I better order my up a pint container from BCS as like you I can't afford a ton. one thing about BCS prices is that the shipping is included in the price so when your looking at UPS being 10 to 20 dollars. But at $.57 cents a pound I would buy a hundred pounds
I can see the cover working in the electric arc furnace because there is no open flame. When you used the limestone did you put it in when you put the crucible in the furnace or after the iron started melting??.
I don't mind pouring aluminum and small quanitiys of brass and such but with Iron like you I have someone here incase something goes wrong, and there are a bunch of things that can. I have plans to set my furnace up so that I can liftout and pour from overhead, that way if I only have phone support someone to call 911 I can pour safely,
The last time I melted iron I made the backing plate, the only thing I put in the crucible waw iron, borax isn't any good with iron that I know of and the only other thing that I had that might of been any extra help in the melt was brazing flux that I have. I can get Fluorspar but like you said its strong stuff and will erode the refactory and your crucilbe. The FeSi I would like to get some and try it, as its suppose to also help with the machineability of the iron. My long reaching plans for this hobby is to eventually learn enough that I can build from scratch a moderate size steam engine, but it looks like as much as there is to have to learn that I may be a very old man before I get there, but I am gonna give it one heck of a try.
So I guess that I better order my up a pint container from BCS as like you I can't afford a ton. one thing about BCS prices is that the shipping is included in the price so when your looking at UPS being 10 to 20 dollars. But at $.57 cents a pound I would buy a hundred pounds
I can see the cover working in the electric arc furnace because there is no open flame. When you used the limestone did you put it in when you put the crucible in the furnace or after the iron started melting??.
I don't mind pouring aluminum and small quanitiys of brass and such but with Iron like you I have someone here incase something goes wrong, and there are a bunch of things that can. I have plans to set my furnace up so that I can liftout and pour from overhead, that way if I only have phone support someone to call 911 I can pour safely,
David and Charlie aka the shop monster
If life seems normal your not going fast enough" Mario Andrette
If life seems normal your not going fast enough" Mario Andrette
Re: cart for my engine
Lots of great information on pouring iron here. Like I said before my own experiences have been very small like 5 lbs or less and no flux at all. This was only a few melts over a year ago. I am about ready to donate my current #10 SiC that is being used for aluminum to iron though and want to cast some dies for future aluminum castings.
I'd rather laugh with the sinners than cry with the saints the sinners are much more fun...
Muller
Muller