Here is my kiln. This is the base:
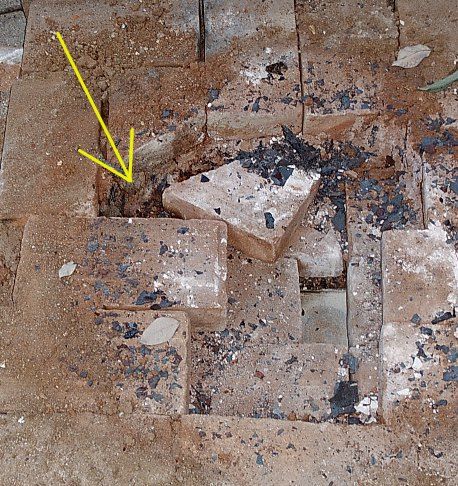
The red arrow indicates the burner hole. The yellow arrow indicates where the heat enters the kiln. there is a wax drip hole you can see with a pan of water under it. The kiln body is a 55 gallon drum covered with 2 inches of ceramic wool, an overcoat of sheet metal, and a 5 inch vent hole in the center of the top.
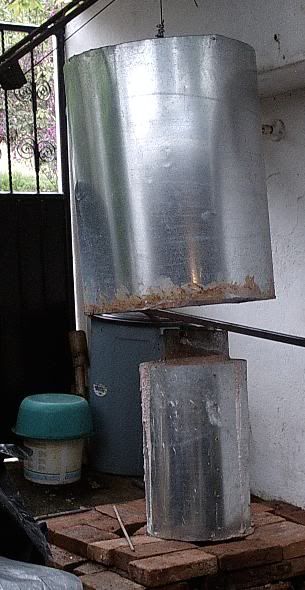
I remove the sheet metal flask from the investment before I burn it out. The investments are reinforced with expanded metal plaster lath which holds them together well.
I generally begin firing at a low flame (propane burner) for several hours to melt the wax. Then I turn it up to a flame that will eventually get the temperature to 1200 F. It takes maybe five or six hours for the kiln to reach that temperature. Then after I have burned it out at 1200 F, I turn off the gas, cover the top vent hole, and fire up the melting furnace. I lift off the kiln a few minutes before the melt is ready to pour so the investment is at least 1000 F when I pour it.
To save fuel, these smaller test pieces I have been doing recently are not burned out in the kiln, but in my large furnace. I place the gas burner in the tuyere, and use a piece of roof tile to deflect the flame around the investment which is elevated off of the furnace floor with a few pieces of broken bricks.
Richard